Product features
- Cast up-to 6 Cavities or 12 Parts Per Cycle/li>
- 96 Air/Water Cooling Lines
- Largest Casting Capabilities
- Multiple Fill Tube Configurations
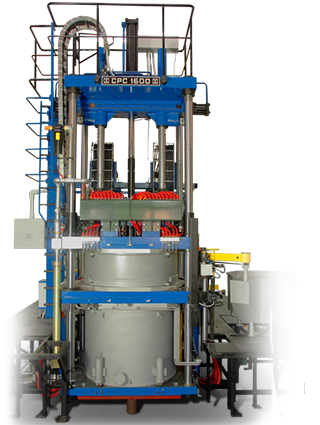
MACHINE CONSTRUCTION
The machine is designed on the same principle that all of our foundry-proven machines have been built. With optimal heavy duty construction on our rugged, vertical four hard chrome-plated steel tie bar and movable plate design, the CPC 1600 gives you even more reliability in difficult foundry conditions.
Larger capabilities and even more castings per cycle
The CPC 1600 has higher productivity then any other chassis casting equipment on the market today. With its 96 air/water cooling lines, you can cast up to six cavities or 12 parts per cycle. The larger platen provides a broad range of capabilities including fitting up to six dies in the die chamber with the ability to cast multiple cavities per die at one time. There is even the ability to change the flanges allowing for different numbers and configurations of riser tubes giving you maximum flexibility.
Cooling System
Up to 96 cooling lines are available per machine to reduce the casting cycle time. We use water boosted cooling up to 10 bars with a reservoir ensuring constant pressure. Each cooling line is independent and can be controlled by time, temperature, or a combination of time and temperature.
We specially designed a flow meter rack that is easily accessible to the machine operator. This allows for the computer-controlled cooling flow to be monitored visually and mechanically.
Ninety-six cooling lines means 192 connections (one inlet and one outlet per line) have to disconnect and reconnect each time a die is changed. We created a die holder with an integrated manifold that automatically connects all 96 cooling lines when the die is operable.
FURNACE
A 900kg electric crucible type holding furnace is available. We understand the importance of using the highest quality alloy possible when casting structure-critical parts. We achieve this by using our specially integrated shuttle system to bring freshly degassed alloy directly to the machine and the crucible type furnace.
CASTING RETRIEVER
An automatic casting retriever transfers the ejected castings out of the working zone of the machine. Extraction may also be done by integration with any of the major robotics manufactured today. The casting retriever can also be safely stowed away as a backup retrieval system when robotics integration is done.
Additional Safety Equipment
Light curtains and electromechanical movable working platforms are used for protection in dangerous areas around the machines.